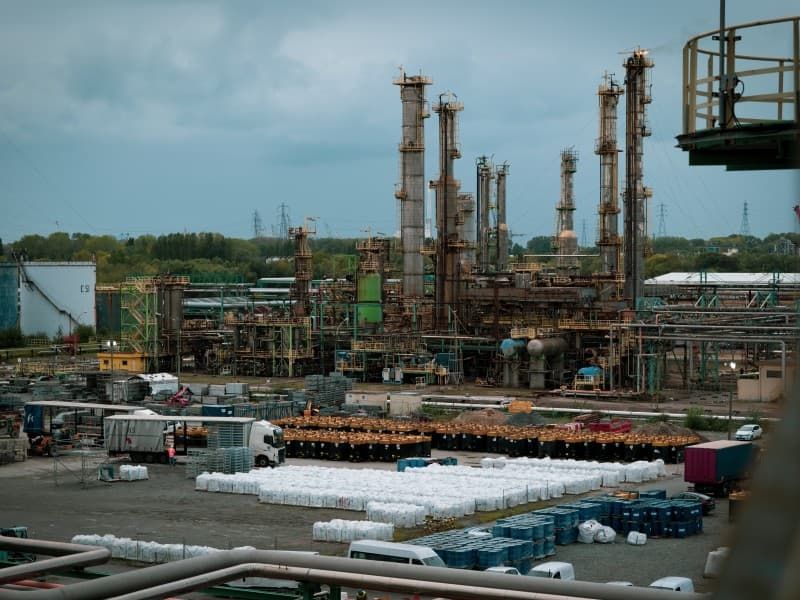
Dense loading and reactor pressure drop
Introduction
Since dense loading reduces the void space within a catalyst bed, it is unavoidable that the bed pressure drop (dP) will increase. This increase is quite significant, of the order of about 80% for a dense loaded bed of extrudated catalyst, compared to a sock loaded bed of the same catalyst. In cases where a reactor already has a problem with pressure drop, this seems to be a serious restriction on proposing dense loading for such a reactor.
However, this situation is not quite as severe as it may appear at first, as will be discussed below. As will also be shown, in some cases dense loading could even offer a solution that will not only give better catalytic performance, but also AT THE SAME TIME relieve a pressure drop constraint, as counter-intuitive as that may sound at first.
Advantages of dense loading over sock loading
Before discussion the pressure drop issue, it will be useful to first review the benefits of dense loading over sock loading:
- Dense loading allows for a greater mass of catalyst to be loaded into a reactor, thus boosting reactor performance through a sheer increase in overall reactor activity.
- Almost as important as the additional catalyst, is the fact that a dense loaded bed is usually more homogeneous than a sock loaded bed, and thus reduces channelling and maldistribution inside the bed. This increases the performance and the run length of any fixed bed reactor.
- During loading, entry into the reactor and onto the bed being loaded is much reduced, with a corresponding improvement in both quality of loading and job safety.
- In many cases dense loading is faster than sock loading, which can be a large advantage when production downtime is costly.
Therefore, due to the tremendous proven benefits of catalyst dense loading, a plant operator should try as much as possible to accommodate a dense loading operation in his reactor change-out strategy. If pressure drop is a concern, the situation should first be evaluated very carefully, and the possibility of doing a dense loading operation should not just be dismissed out of hand.
Bed pressure drop versus reactor pressure drop
In the first place, the increase of 80% mentioned above only applies to the catalyst bed itself – all other dPs in the circuit (inlet diffuser, distribution and mix trays, outlet collector etc.) are unaffected. Thus, the percentage increase in the overall reactor circuit dP will be smaller, depending on the relative dPs of these other items.
On reactors where these other pressure drops are very significant, the effect of the catalyst bed may not be too constraining, especially when taking into account the effect of natural bed compaction, as discussed below.
Effect of the bed settling
Secondly, the 80% increase in dP refers to the situation at Start of Run (SOR), in other words comparing a dense loaded bed as SOR with a sock loaded bed also at SOR. However, a high reactor pressure drop typically causes constraints on pump and compressor capacities at End of Run (EOR), not SOR, and thus it is much more pertinent to compare the pressure drop of a dense loaded bed and a sock loaded bed at EOR.
It is well known that virtually all sock loaded reactors experience significant settling (compaction) of the catalyst bed during the cycle, which can be as high as 10%. By contrast, since a dense loaded bed is already at maximum density, such a bed does not experience any settling during the cycle. Therefore, a large portion of the pressure drop increase that is observed in sock loaded reactors from SOR to EOR, in fact comes from this compaction of the bed, which is not applicable to the dense loaded bed.
Of course, the EOR dP is also affected by other factors such as coking of the bed and the accumulation of external contamination, which are the same for both sock and dense loaded reactors. Therefore, most reactors will experience an increase in pressure drop over the cycle, but this increase is much slower for the dense loaded bed than for the sock loaded one. This is illustrated in the following graphs.
Evolution of pressure drop during a run cycle
Since the accumulated pressure drop at EOR is the result of many factors (coking, external contamination, etc.), with varying degrees of influence depending on circumstances, it is not possible to give a precise value for the increase of the dP of a dense loaded beds at EOR. However, it is of the order of about 20 – 40%, and certainly much lower than the 80% at SOR.
Strategy for dense loading a high dP reactor
However, even this degree of dP increase may be too much for some marginal reactors. Fortunately there exists a strategy that could be employed in some instances, which could bring the benefits of dense loading even to these reactors. This entails dense loading a larger size of the catalyst, and is contingent on the availability of the catalyst in question in a larger size (preferably about double the size).
The principle is that, although the larger catalyst will probably have a lower relative activity (RVA), by dense loading the same bed VOLUME, a larger MASS of catalyst can be loaded into the reactor. The increase in mass should more than compensated for the loss of RVA. At the same time, the larger size will dramatically reduce pressure drop, even if it is dense loaded. This is best demonstrated by means of a worked example of a hypothetical case.
Consider a reactor with a sock loaded bed containing 100 tons of a 1.5 mm extrudate catalyst. As this is the base case, the activity and dP are both assigned a value of 100. The final target is to have a dense loaded bed of the same catalyst, in a larger size. It will be approached with a two-step analysis. NB: this two-step approach is only a calculation procedure to illustrate the concept, it does not have any significance for the actual implementation of this strategy.
As a first step, consider the effect of changing the catalyst to the identical type with respect to chemical composition, but double the size, i.e. an extrudate of 3 mm diameter. The reactor is still sock loaded. Assuming an equal L/D ratio for the two catalyst sizes, the packing factor will be the same and thus the catalyst inventory will be the same (100 tons). This will reduce both the pressure drop and the overall activity of the bed. For this example an activity reduction of 10% will be assumed, and the reduction in pressure drop at a ratio of 1:3.
Both these assumed values are more or less based on reality. The reduction in bed activity reflects an RVA number of 90% for the larger sized catalyst, as per estimates from a few catalyst suppliers. The pressure drop reduction is more difficult to estimate (the Ergun equation is notoriously difficult to apply in two-phase systems). Nevertheless, using the limit values of the Ergun equation, the pressure drop reduction should be somewhere between 1:2 and 1:4.
Applying these factors to the base case, gives the following values for the sock loaded larger size catalyst: bed activity 90, bed dP 33.3.
As a second step, the loading process for this larger size catalyst is now changed from sock to dense loading. As a result, more catalyst will be loaded, and at the same time the bed pressure drop will increase. Applying the typical factors for the increase in density (=weight of catalyst) of 15%, and an increase in dP of 80%, the reactor will now have an overall activity of 90 X 1.15 = 103.5, and a dP of 33.3 X 1.80 = 60.
This example is summarised in the following table:
BASE CASE | INTERMEDIATE STEP | FINAL SITUATION | |
---|---|---|---|
Type of loading | Sock | Sock | Dense |
Size of catalyst (mm) | 1.5 | 3.0 | 3.0 |
Catalyst inventory (tons) | 100 | 100 | 115 |
Bed activity | 100 | 90 | 103.5 |
Bed dP | 100 | 33.3 | 60 |
Summary of results from example calculation
In the example above, and as a result of the scaling factors used for pressure drop and catalyst activity, it appears that the strategy will give not only a small increase in activity, but also a very significant reduction in bed dP.
Even if the assumptions were too optimistic
Naturally, each case will have to be carefully examined for the validity and feasibility, and appropriate scaling factors applied for the particular reactor and service under investigation. This strategy must also be discussed in detail with the catalyst vendor.
Nevertheless, even if no improvement in either the activity or the pressure drop is observed, and the dense loaded bed of larger size catalyst only gives exactly the same SOR performance as the sock loaded bed of the smaller sized catalyst, the dense loaded bed is still much superior on two counts:
- By virtue of its more homogenous loading, the dense loaded bed will be less likely to suffer maldistribution, as discussed above.
- The dP of the dense loaded bed will be more stable over the duration of the run, and not prone to the settling and increased pressure drop usually present in sock loaded beds. Therefore, even if the dense loaded bed has the same dP as the sock loaded bed at SOR, at EOR the pressure drop of the dense loaded bed will probably be significantly lower. This could be a very significant benefit, since this whole analysis was done due to the reactor being pressure drop limited in the first place.